Ship launching airbags are to be constructed of a cylindrical body and two conical heads (one at each end). Ship launching airbags with lots of advantages, such as easy to operate, time saving, saving investment safety, etc.
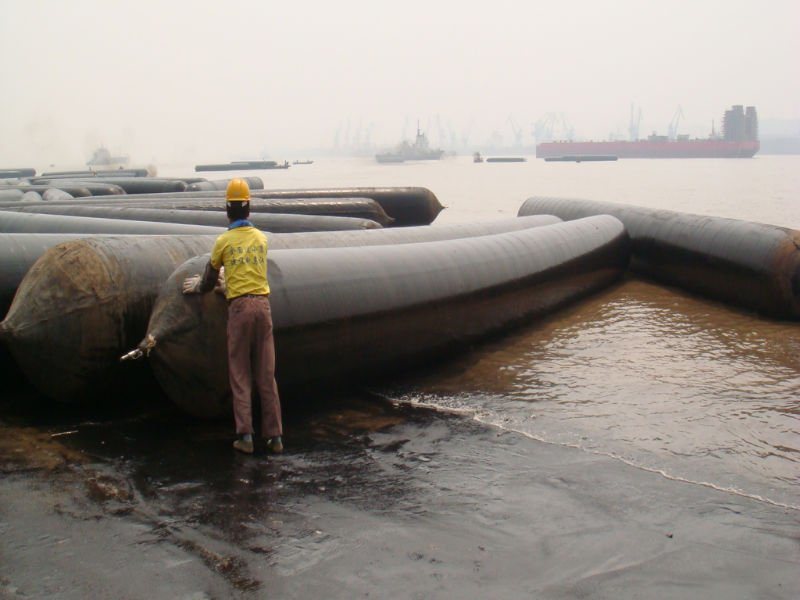
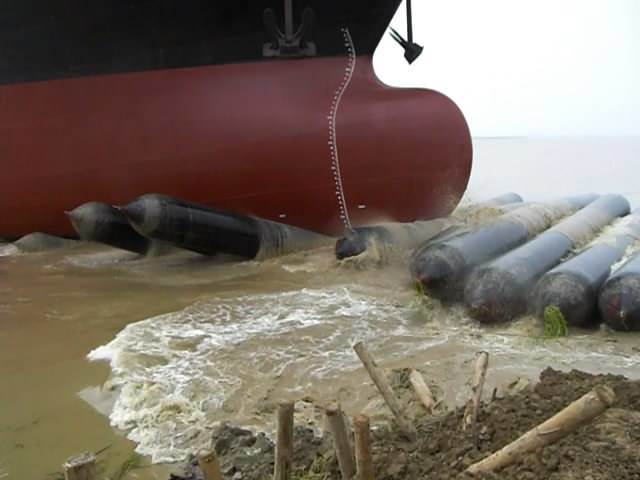
Major Strengths of Ship Launching Airbags:
High level of safety: Equipped with a reliable safety valve, our airbags can stand the maximum pressure up to 4 times that of the operating pressure.
Good air tightness: Pressure decreases less than 10% for a period of 24 hours.
Long lifespan: It is guaranteed that our airbags can sustain their designed operating pressure for 3 years.
Specification
1. Structure
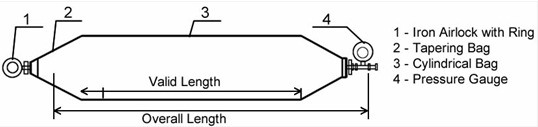
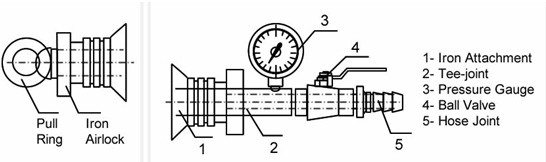
2. Diameters: 0.8 m - 2.0 m or customized.
3. Length: 6 m - 20 m or customized.
4. Loading Capacity: about 10 T/M to 40 T/M.
5. Grades:
Ordinary airbags - 3, 4 or 5 layers of synthetic-tire-cord.
High bearing capacity airbags - 6, 7 or 8 synthetic-tire-cord.
Super high bearing capacity airbags - 9, 10 or more layers of synthetic-tire-cord.
6. Accessories: Pull ring, iron airlock, tee joint, pressure gauge, ball valve, hose joint etc.
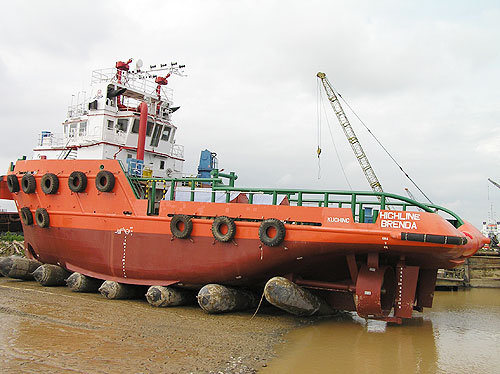
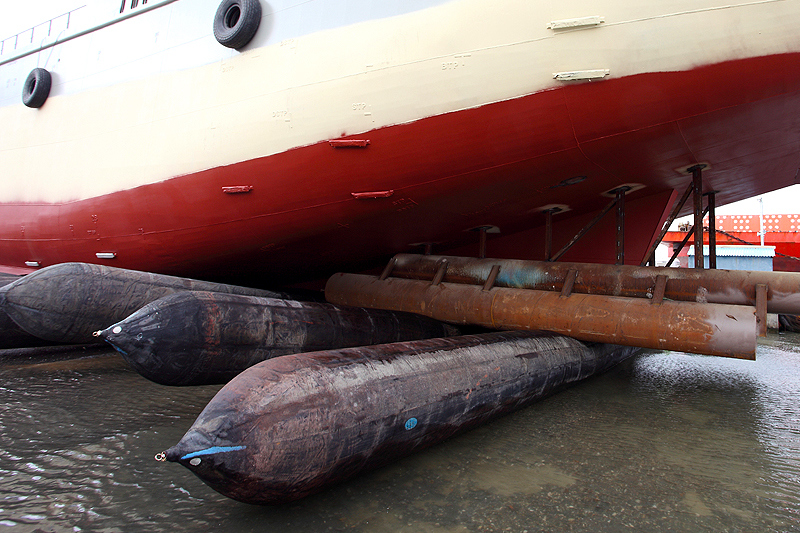
7. Technical Data of Ship Launching Airbags
Model | Diameter (m) |
Initial pressure (KPa) |
Rated working pressure, Pe (KPa) |
Bearing capacity (kN/m) | Minimum burst pressure (KPa) |
QP3 | 0.8 | 25 | 130 | 114 | 390 |
1.0 | 18 | 100 | 110 | 300 | |
1.2 | 15 | 85 | 112 | 260 | |
1.5 | 13 | 70 | 115 | 210 | |
QP4 | 0.8 | 35 | 170 | 149 | 510 |
1.0 | 25 | 130 | 143 | 390 | |
1.2 | 20 | 110 | 145 | 330 | |
1.5 | 16 | 90 | 148 | 270 | |
1.8 | 14 | 80 | 158 | 240 | |
QP5 | 0.8 | 48 | 210 | 184 | 630 |
1.0 | 35 | 170 | 186 | 510 | |
1.2 | 28 | 140 | 185 | 420 | |
1.5 | 20 | 110 | 181 | 330 | |
1.8 | 16 | 90 | 178 | 270 | |
QP6 | 1.0 | 45 | 200 | 219 | 600 |
1.2 | 32 | 165 | 217 | 490 | |
1.5 | 25 | 130 | 215 | 390 | |
1.8 | 20 | 110 | 218 | 330 | |
Note: 1. Rated working pressure:±5%. 2. Compress deformation: ±2%. 3. Bearing capacity: one meter airbag at a deformation rate of 70%, internal pressure equivalent to the rated pressure value of Pe. |
9. Rubber Material Test:
No. | Test item | Required value | Test method | |
1 | Tensile Strength, MPa | ≥ 18 | ISO37 | |
2 | Elongation at break, % | ≥ 400 | ISO37 | |
3 | Hardness, shore A | 60±10 | ISO7619-1 | |
4 | Tear Strength N/cm | ≥ 400 | ISO34-1 | |
5 | Compression set, % (70 ºC ± 1 ºC, 22 h) | ≤ 30 | ISO815-1 | |
6 | After thermal aging at (70 ºC, ±1 ºC, 96 h) |
Holding of pull lengthening,% | ≥ 80 | ISO188 |
7 | Holding of elongation at break,% | ≥ 80 | ISO188 | |
8 | Change of hardness, hardness | ≤ 8 | ISO7619-1 | |
9 | Static ozone aging at 40 ºC*96 h, {ozone concentration( 50±5)*10} |
No crack | ISO1431-1 |
10. Reinforcing Material: the warp should be (90±5) cord per 100 mm in width, and the breaking strength shall be more than 205 N per cord.
Â
11. Appearance: The appearance of an air bag shall be smooth, glossy and without blemish such as crack, blister, delamination pits or impurities.
Â
12. Dimensional Tolerances:
The length and diameter of an airbag shall be measured with the rated working pressure and be within ±3%.
Â
13. Ship Launching Airbags Performance:
D (M) |
(4-5 layers) | (6-8 layers) | Â | ||
Initial pressure (MPa) |
Working pressure (MPa) |
Initial pressure (MPa) |
Working pressure (MPa) |
 | |
 | |||||
1.0 | 0.14 - 0.16 | 0.12 - 0.14 | 0.22 - 0.26 | 0.20 - 0.24 | Â |
1.2 | 0.12 - 0.14 | 0.10 - 0.12 | 0.20 - 0.24 | 0.17 - 0.22 | Â |
1.5 | 0.10 - 0.12 | 0.08 - 0.10 | 0.15 - 0.20 | 0.13 - 0.18 | Â |
1.8 | 0.08 - 0.10 | 0.07 - 0.09 | 0.13 - 0.16 | 0.11 - 0.14 | Â |
2.0 | 0.07 - 0.09 | 0.06 - 0.08 | 0.12 - 0.15 | 0.10 - 0.13 | Â |
Â
PPR sockets must be manufactured and designed to be compatible with all PPR piping systems. How do you do fusion PPR? It will be pointed to one fusion welder named ppr socket welder. PPR socket fusion welding is a widely used technique for assembling plastics piping systems using injection moulded fittings. Socket welder is mainly for ppr/hdpe pipe and fittings butt-fusion. This socket fusion tool set contains everything required to perform fusion jointing on site. Suitable for all commonly used plastics and featuring a long service life, This PPR socket fusion welding machine guarantees extremely accurate temperature control for strong, consistent joints. PPR pipe welding Machine are all the major part are made of high-quality materials, simples operation, convenient and practical, its ideal for pipeline construction equipment. Wuxi Yuda produces RDS32/20, RDS63/20, RDS110/75 and RDS160/63 portable ppr/hdpe pipe socket fusion welder, also RDS-T160 manual socket fusion machines. Installing PP-R Products using Socket Fusion: Step 1 – Match Pipe and Valve Size, Cut Pipe Step 2 – Inspect the Cut Step 3 – Measure Pipe Insertion Depth Step 4 – Prepare Welding Iron Step 5 – Heat Outside of Pipe and Inside of Fitting Step 6 – Insert Pipe in Fitting Step 7 – Allow Welded Connection to Cool Step 8 – Verify Connection
Socket Welder,Socket Fusion Welding,Socket Welding Machine,Socket Fusion Welding Machine
WUXI MEIERTE MACHINERY TECHNOLOGY CO.,LTD , https://www.pipefusionwelding.com